GREENCASTLE, PENNSYLVANIA — At a dual-monitor computer in the office of the XPO Hagerstown terminal just off Interstate 81, freight operations supervisor Kylee Garnett tracks dockworkers’ productivity and drivers’ progress on their routes in real time.
XPO’s labor management software helped determine the terminal required more forklifts, which the carrier shifted over from a shop in nearby Western Maryland last month. And its route optimization platform is particularly helpful to dispatchers, because about two-thirds of pickup requests come after trucks have already been dispatched.
“We’re always on the phone,” Garnett said, within minutes of her phone ringing.
A tour of the Hagerstown facility, one of XPO’s largest in the country, and a drive in one of the company’s trucks provided glimpses of how the company uses its vaunted technology to maximize visibility and efficiency across its network.
Jay Silberkleit, who succeeded Mario Harik as CIO upon Harik’s ascension to CEO, talks about graph theory, the butterfly effect and constantly tweaking algorithm knobs to optimize freight movement across the company’s 297 terminals and 67 freight assembly centers.
But he assures Transport Dive readers: “It’s not that complicated.”
“In LTL, it's all about optimizing how you flow freight through the network, where you should be building that density, how you can reduce miles in the network,” he said.
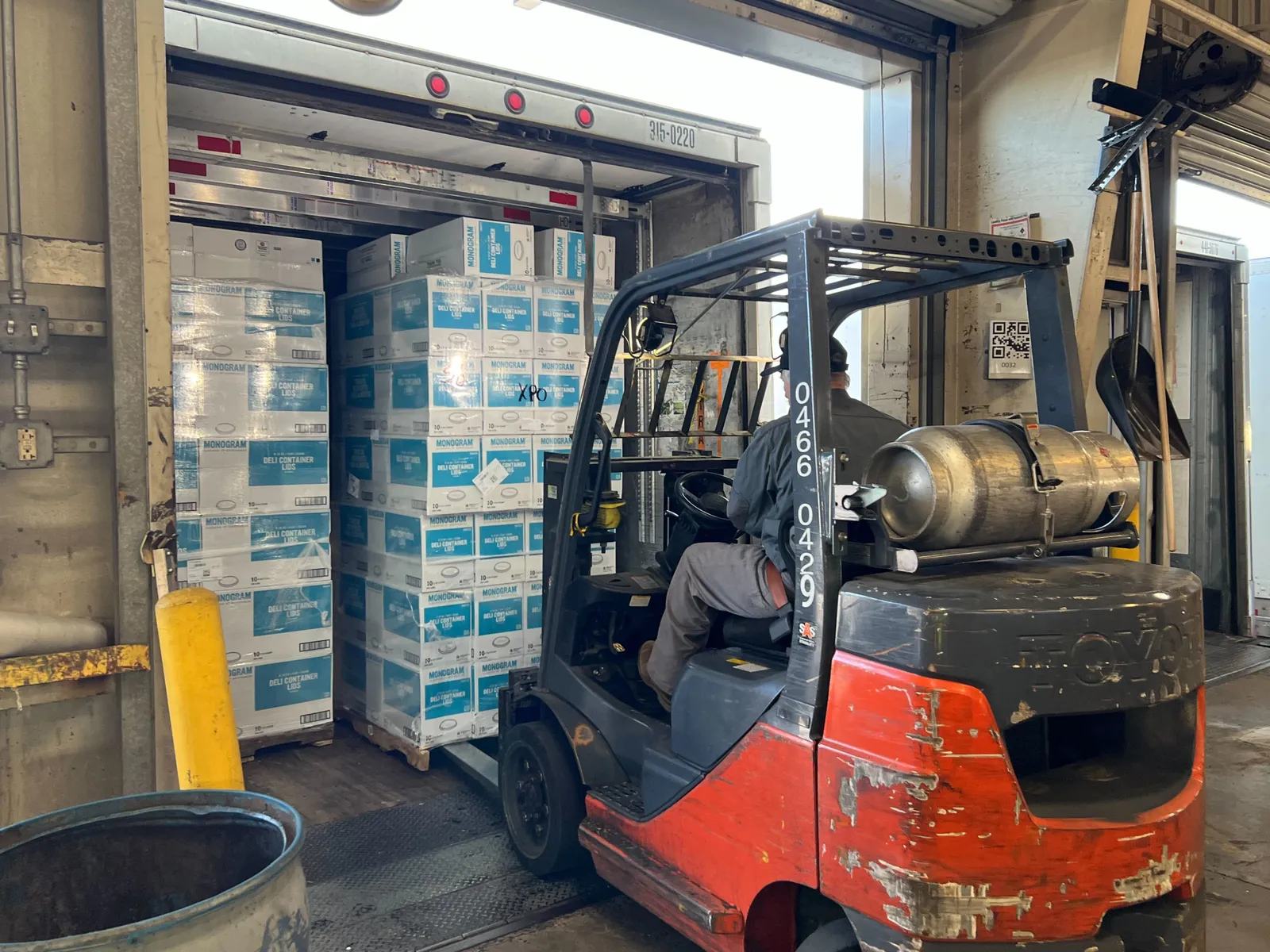
On the dock: Handheld devices and QR codes
During the visit, one dockworker in a forklift loaded pallets of Monogram deli container lids into a waiting trailer. Each dockworker is equipped with a handheld scanner, which tells them where each load goes.
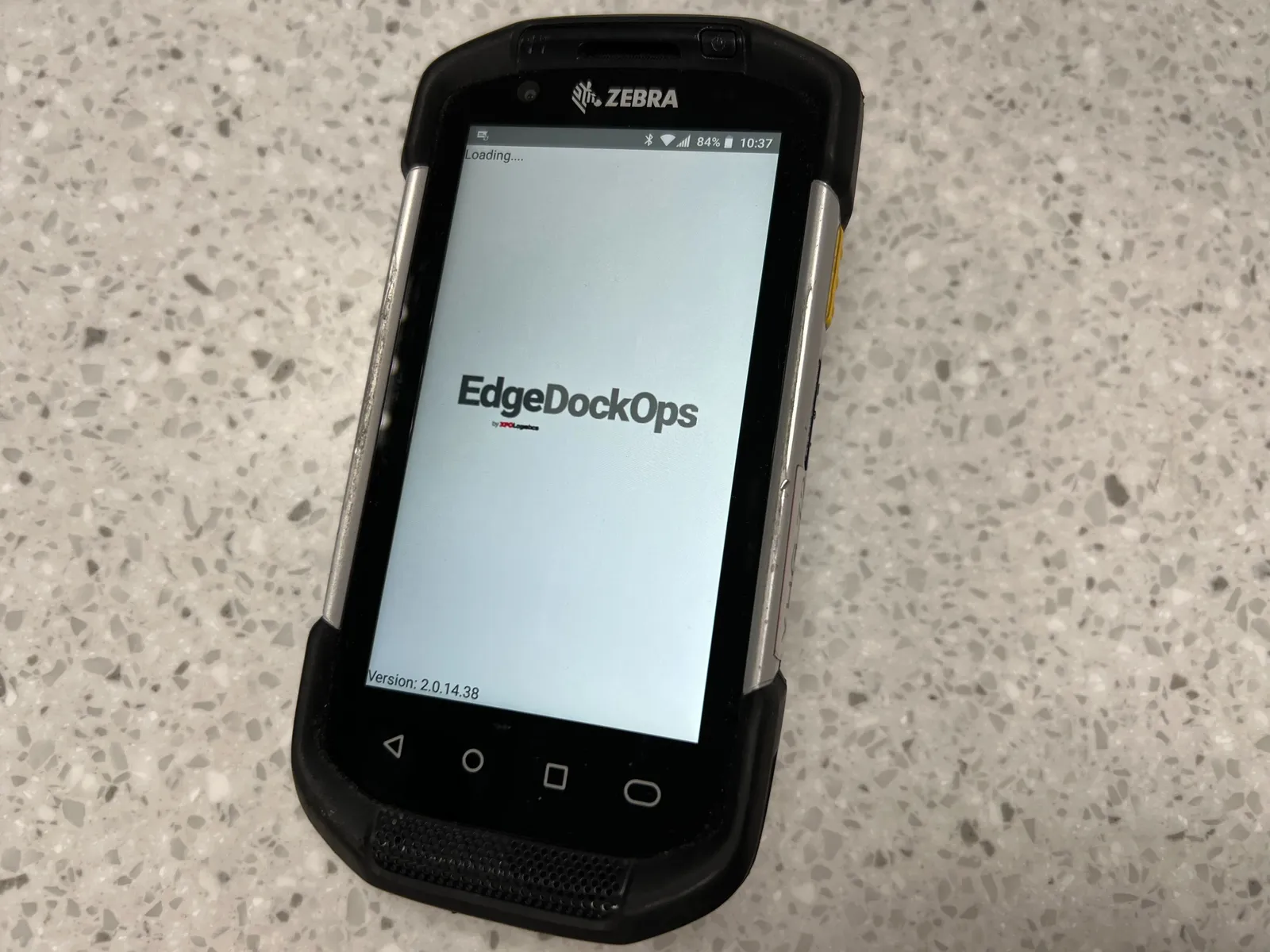
The scanners also report metrics to XPO. Among them: the number of minutes from a dockworker’s clocking in to their first pallet being scanned, and the number of minutes between each scan.
Aroon Amarnani, vice president of strategy and sustainability, said the labor management system is intended to help better schedule the terminal’s workday, which is busiest overnight.
“As silly as it sounds, if you line up labor correctly, you're basically freeing up time, rather than having some people waiting, like the drivers waiting for the dockworkers to come and unload,” he said. “If you line that up properly, you're actually unlocking capacity.”
QR codes are above each terminal door and, more recently, on each pallet, to simplify dockworkers’ jobs and provide the carrier better visibility into its operation. Labeling each pallet is intended to bring benefits for customers and drivers, too, mitigating issues such as drivers delivering three of four expected pallets to a customer.
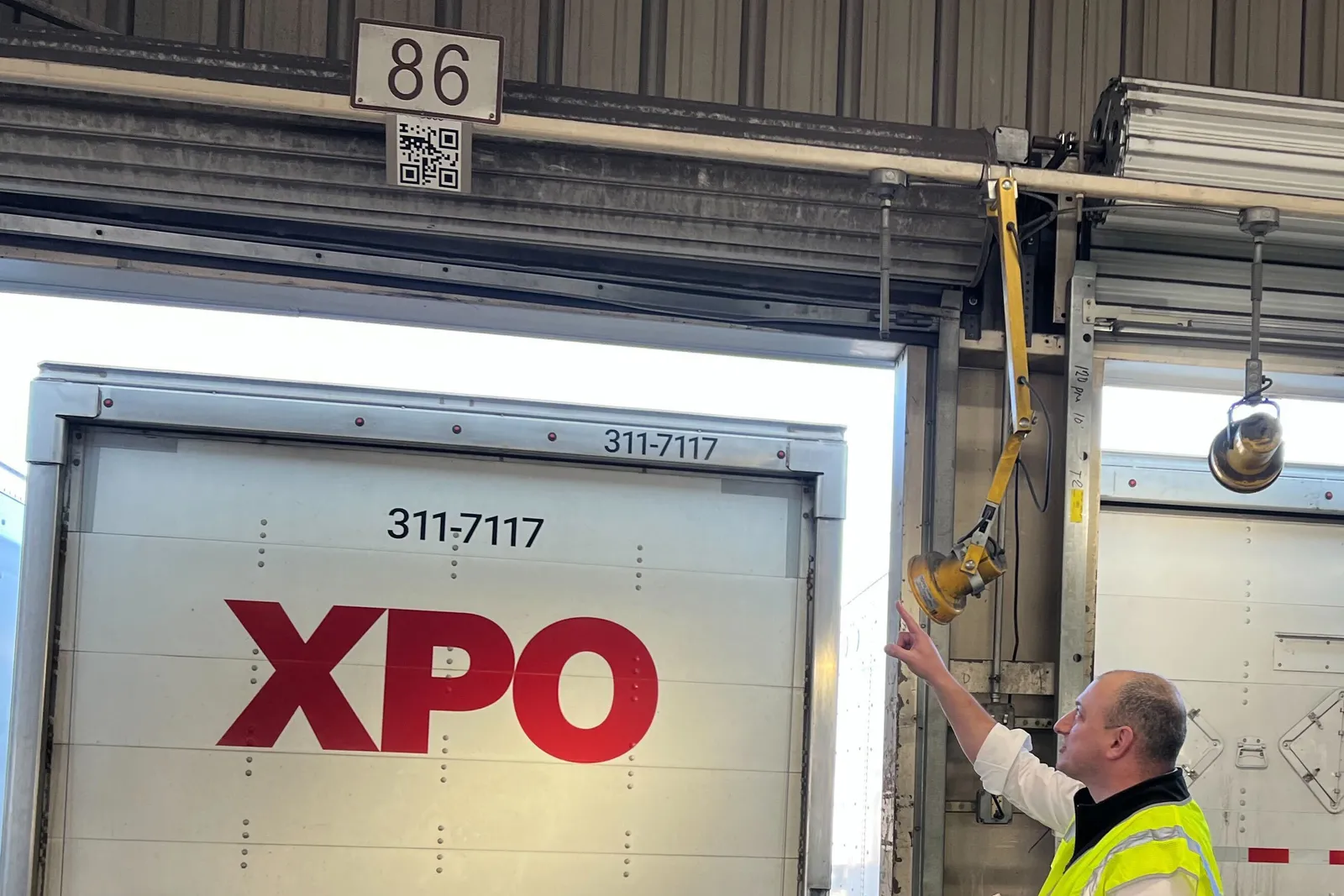
In the truck: Harsh brake alerts and real-time pickup request updates
Under XPO driver trainer Don Giffin’s oversight and encouragement, I put the pedal of a 2022 Freightliner Cascadia to the floor.
The automatic-transmission truck rumbled, with an empty 28-foot trailer (a “pup”) in tow, across the terminal’s large parking lot.
I hadn’t asked or expected to ride in a truck during the terminal visit — much less, drive one and learn how to put it in reverse.
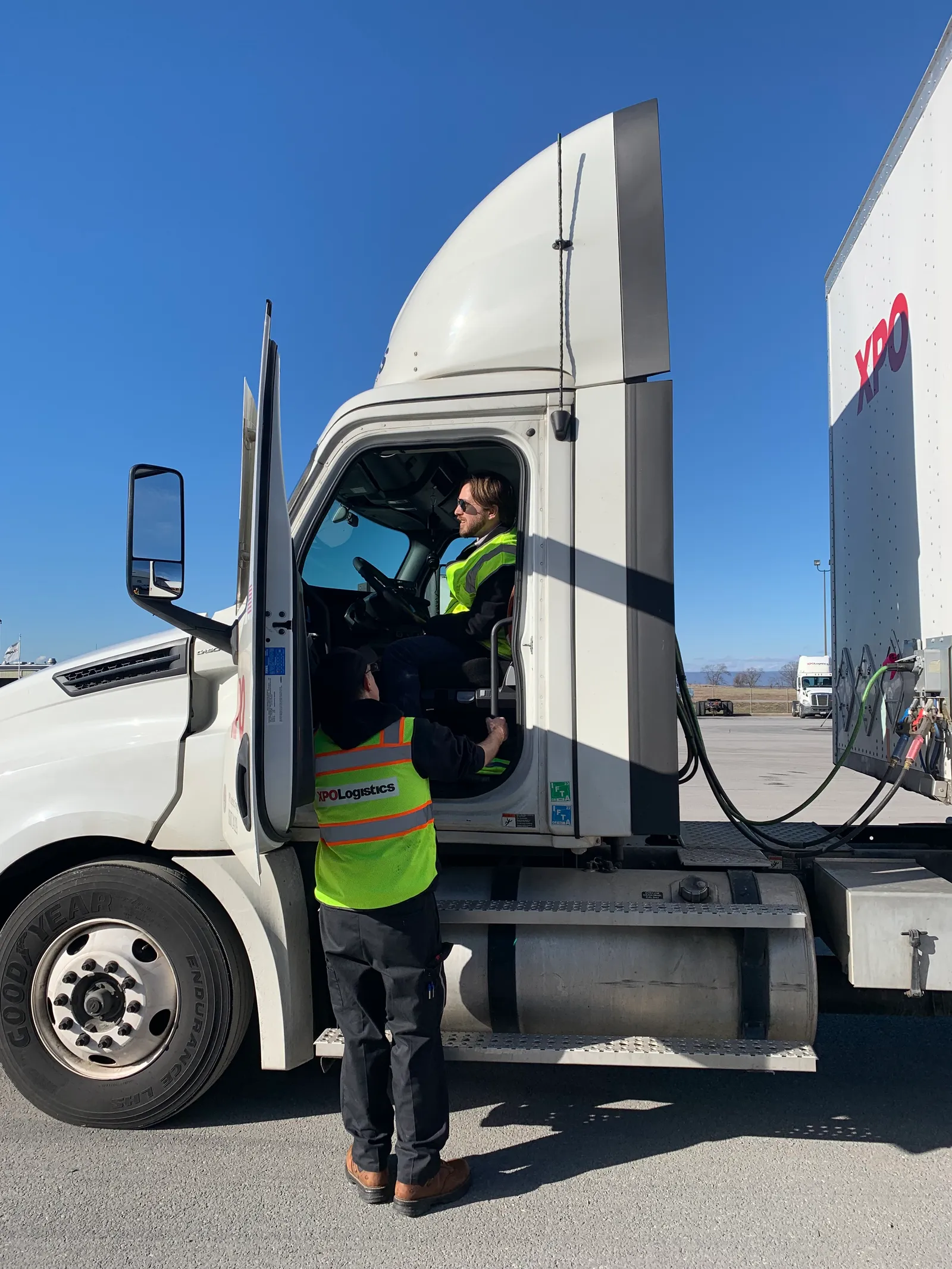
But, thanks to “Giff,” as he’s known, I was in for one more surprise. And it provided another reminder of how far XPO’s technology extends its sight line into its operation.
“Hit the brakes hard,” he instructed from the passenger seat, just as the truck picked up speed.
I slammed the brake pedal.
“Harsh event detected,” an alert informed us, as the truck ground to a halt.
The company received a similar alert, along with the footage of the five seconds before the event and five seconds after it, from a driver-facing and outward-facing camera.
Back in the terminal office, Garnett pulled up a digital map of the region that includes trucks’ optimized routes and useful geo-overlays of each XPO terminal’s service area. She showed how the technology displays the drivers’ progress, reported via GPS on the trailers, and demonstrated the process of communicating additional pickups or drop-offs to a driver who has already hit the road.
“I enjoy the challenge of getting things covered,” Garnett said. “We have a great team. ... Every day is different.”
Source: Travis Hinckle, senior service center manager, XPO Hagerstown terminal